Realize indium coating film R Technology
Indium mirror coating system
R technology is the ultimate thin-film coating technology. Indium plating-like coating "ECO MIRROR 49" is formed into a thin film coating using R technology.Plating-like coating by spraying is realized.
Reproduction of thin film by R technology. Plating-like coating is realized.
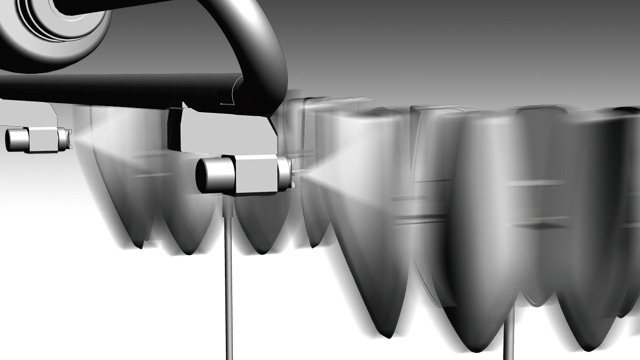
The growing demand for plating is not just for design, but also for parts that combine functionality, such as communications, making it important to reproduce metal coatings that meet functional requirements.
Therefore, Takubo Engineering's original thin-film coating technology with revolving coating, "R technology," replicates it.
Automatic spray guns, robots, controllers, conveyors, precision paint feeders syringe pumps, software SWANIST, etc. are controlled by advanced collaborative technology. By accurately reproducing the coating conditions set by SWANIST, a high-quality thin-film coating film can be completed at a low cost. The plating-like coating is achieved by digital coating with numerical control.
Plating-like coating realized by technology cultivated in revolving coating In. Mirror Coating System
Thin-film coating with R technology is the key to plating-like coating
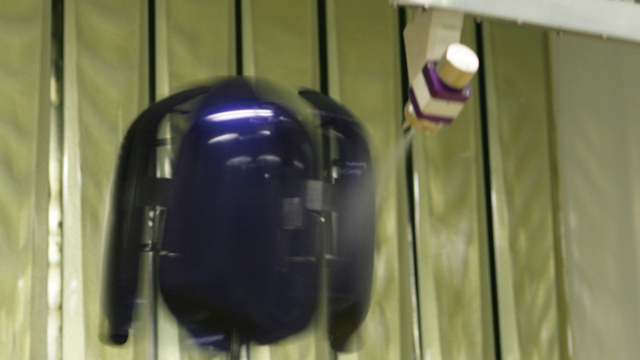
Indium coating is a film that combines functionality, such as millimeter wave permeability, in addition to design properties. It is important to realize a thin film to take advantage of this feature. The R technology of spray painting and thin-film multiple coating realizes the film.
R technology Indium coating process

The painting process of the In. Mirror Coating System consists of three coats: under, indium, and top. The plating-like coating is made feasible by the indium coating in the middle coat. Thin, discontinuous films are formed to perform functions such as transmitting millimeter waves. R technology makes it possible to mass-produce it in sprays.
The robot coats the workpiece while revolving it forward and backward, reproducing thin-film multiple coating. R technology numerically controls all condition settings from robot to spray, rotation speed, etc. It realizes thin-film digital coating.
R technology Thin-film multiple coating
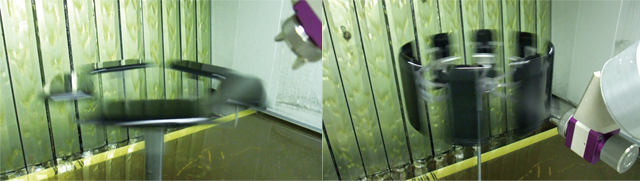
The workpiece is mounted on a circular jig and the transfer device of the robot system with rotation mechanism rotates forward and reverse.
The robot repeatedly applies multiple thin-film coatings to the rotating workpiece.
R technology Condition setting
- Coat large areas of the workpiece with a wider pattern / Coat a narrower pattern on the part that hits the back side of the workpiece A series of condition settings are easily controlled by setting teaching conditions. You can freely change the pattern as if you were editing a video.
R technology Flexible condition setting - In revolving coating, the work is distributed between the revolving workpiece and the robot, simplifying the robot's movements and reducing robot costs by requiring only four axes on the robot itself. In addition, the fewer the number of axes, the simpler the robot control (teaching) and the easier the condition setting work becomes.
R technology Logo mark - The features of revolving coating are as follows.
・Cooperative work between workpiece and robot
・Robot movements are simple and easy to teach.
・Coating can be done by 4-axis robot
・No programming of the robot is required but can be done by inputting SWANIST's numerical values (setting conditions)
Precise dosing of paint Paint supply system syringe pump
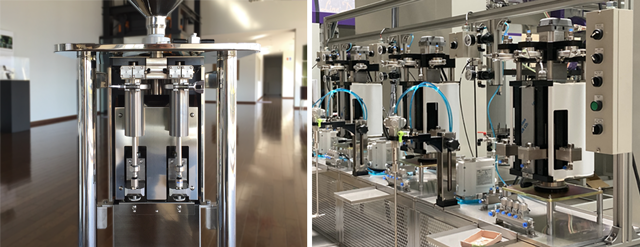
A paint feeder for spray painting systems that simultaneously solves quality, cost, and environmental issues is essential. A syringe pump system is systematized to control the paint ultra-precisely and deliver the required amount to the gun precisely as required.
Flexible film thickness control. Software to simplify condition setting
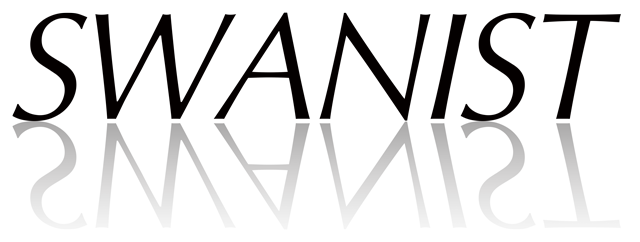
Controlled by “SWANIST” software that reproduces thin-film coating. SWANIST is an assistant software program that provides sophisticated programmatic control of painting equipment. This software simplifies the setting of coating conditions and quantifies and manages the coating process.
Tools for digital coating Teaching Assistant Software “SWANIST”
- The Role of the SWANIST
Equipped with SWANIST Controller Image (SWAN) - Robot Teaching
- Set spray conditions such as discharge volume, atomization pressure, pattern pressure, etc.
- Management of coating data including teaching data
- Automatic workpiece placement, 3D simulation
- 3D virtual coating simulation
- Control of paint usage, production, and coating time
- Control of peripheral equipment such as jig rotation speed, spray conditions, robot trajectory, etc.
Coating jig
Critical to quality and cost Revolving jig development
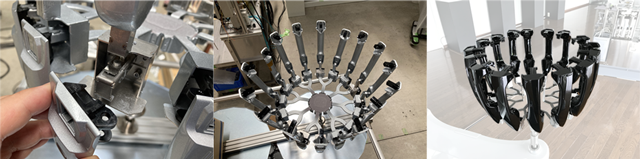
●Workpiece removability ●Handling ●Productivity ●Ease of Coating ●Coating cost, etc. The coating jig reduces coating time by restricting unnecessary robot movements. This is an important factor affecting the coating cost.
Key Points for Jig Development
1)Installation angle to reduce unnecessary robot movement
2)Arrangement that allows spraying to reach every corner of the workpiece
3)Productive number of installations
4)Ease of installation and removal
5)Good handling
6)Stain-resistant construction
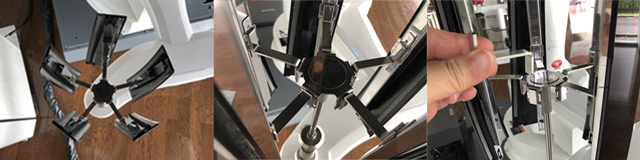
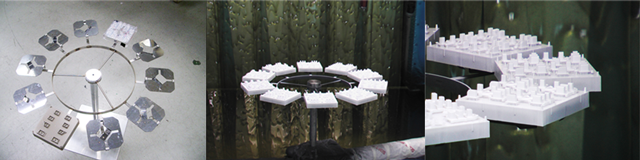
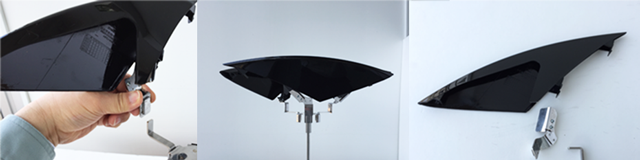
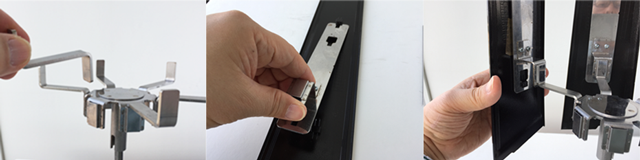
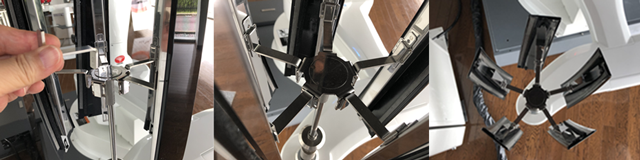
Any workpiece and any material
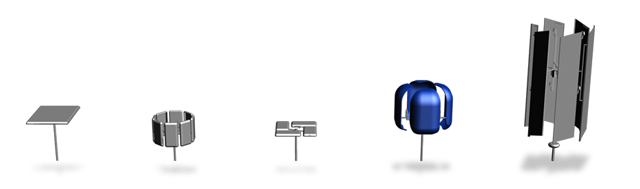
In. Mirror Coating System is suitable for all kinds of workpiecesSizes range from medium to small. From mobile communication devices to home appliances, cosmetic and cosmetic parts. A wide range of materials are available, including ABS, PC, glass, and stainless steel.

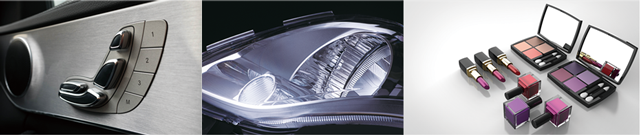
Visualization of coating by fluid analysis

R technology visualizes and analyzes coating efficiency and coating time using fluid analysis technology. By quantifying the optimum conditions, the superiority of revolving coating is also demonstrated.
Standardization of R technology
Free from the heavy workload of the spray man. “R technology”, which makes maximum use of the robot's strengths of unrelaxed motion and repetitive accuracy to revolving coating of workpieces, aims to standardize robot coating. Good thin-film coating finish, high productivity, low paint usage, and significant reduction of VOCs are possible. “R technology," which uses sophisticated applications to control the peripherals required for coating.
We will pursue a world that eliminates globally distributed production risks, improves environmental performance, DXing of FA, and even AI-based simulation.
2023.01.19